|
|
|
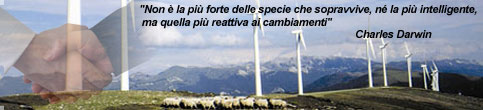
BIOMASSE
DIVISIONE BIO-ENERGY
.:
Richiedi contatto per approfondimenti, un preventivo, una prefattibilità e/o uno studio di fattibilità >>
.: La Cogenerazione
La cogenerazione è una soluzione impiantistica finalizzata ad aumentare l’efficienza dei processi di produzione energetica grazie alla generazione simultanea di energia elettrica e termica partendo da una singola fonte di energia primaria. I sistemi di cogenerazione generalmente prevedono un unico impianto integrato, costituito da un motore primario, che trasforma l’energia chimica del combustibile in energia meccanica, un generatore, che converte l’energia meccanica in energia elettrica e un sistema di recupero termico, che recupera il calore da diversi punti del motore primario, rendendolo fruibile. La cogenerazione si basa quindi sul riutilizzo del calore generato durante la fase di produzione di energia elettrica.
La micro cogenerazione è l’applicazione dello stesso principio a impianti di piccola taglia, tipicamente da poche decine di kW a 1 MW, generalmente installati in prossimità di utenze finali.
L’energia termica recuperata può essere utilizzata in diversi modi, tra i quali: in processi produttivi industriali, per riscaldamento o rinfrescamento di edifici, per produrre ulteriore energia elettrica.
Il rendimento complessivo di un impianto di cogenerazione è nettamente superiore rispetto a quello che si avrebbe dalla produzione separata delle diverse forme energetiche.
Gli impianti cogenerativi ovvero trigenerativi (producono energia frigorifera mediante gruppi ad assorbimento) possono essere alimentati da oli vegetali ovvero syngas, entrambe fonti rinnovabili e aventi diritto ad usufruire delle tariffe incentivanti da parte del GSE (tariffa onnicomprensiva o certificati verdi), destinate agli Impianti Alimentati da Fonti Rinnovabili (IAFR).
Olio vegetale e motori
Fra le biomasse, una parte importante è costituita dagli oli vegetali ottenuti per estrazione o frangitura da semi di specie vegetali dette appunto oleaginose (mais, girasole, colza, soia, palma per citarne solo alcune).
Il primo motore della storia, realizzato da Rudolf Diesel nel 1892, era alimentato a olio vegetale. Solo in seguito si è passati al combustibile di origine fossile che garantiva caratteristiche di fluidità e maggior potere calorifico.
Dopo circa un secolo, i costi raggiunti dai prodotti petroliferi, uniti ad agevolazioni economiche legate agli obiettivi di riduzione dei gas serra previsti nel Protocollo di Kyoto, hanno reso l’uso dei biocombustibili sempre più competitivo.
L’olio vegetale che può essere utilizzato in tali tipi di motori per produzione energetica può essere di derivazione diretta dal seme oleaginoso o può derivare dal recupero di oli vegetali usati per altri scopi. Nel caso della produzione diretta, generalmente si utilizza l’olio di colza, girasole, soia, palma o jatropha.
L’utilizzo di un impianto a olio vegetale, se comparato con un impianto a combustibile fossile, permette una riduzione delle emissioni gassose prodotte dai motori. Consente inoltre l’azzeramento del bilancio globale dell’anidride carbonica: la CO2 prodotta durante la combustione degli oli vegetali è compensata da quella utilizzata nel processo di fotosintesi dalle colture oleaginose stesse. Studi indipendenti mostrano che, confrontando l’anidride carbonica emessa durante tutto il ciclo di vita dell’olio vegetale con quello del gasolio, si ha un risparmio complessivo medio di 2.5 tonnellate di anidride carbonica per ogni tonnellata di gasolio sostituito.
Per quanto riguarda le emissioni gassose, la combustione di oli vegetali è migliore grazie alla presenza di ossigeno all’interno della sua molecola, che non contiene inoltre idrocarburi policiclici aromatici e zolfo, si ha quindi una riduzione degli inquinanti e della pericolosità delle emissioni. Si ha inoltre una diminuzione anche delle emissioni di particolato fine (PM10) e di monossido di carbonio.
SYNGAS
La conversione dell’impianto per l’utilizzo come pirogassificatore ha il grande vantaggio di non precludere la possibilità di funzionamento ad olio vegetale e di fornire una valida alternativa in caso di futuri imprevedibili aumenti dell’olio vegetale combustibile, a seguito di un proporzionale aumento dei carburanti di origine fossile.
L’impianto bi-fuel, pur impiegando un motore della potenza nominale di 260 kW, eroga solamente 200 kW di potenza di picco. Per tale motivo, gli impianti bi-fuel da 1 MW, impiegano 5 moduli invece dei 4 necessari per gli impianti ad olio vegetale standard.
Il prezzo maggiormente elevato dell’impianto bi-fuel viene compensato dal costo estremamente contenuto del carburante, che è pari ad € 0,15 euro/kg. Tale prezzo è stato valutato, considerando acquisti programmati di quantità considerevoli di pellet di prima qualità.
Tale soluzione tiene principalmente conto del fatto che il prezzo del pellet, nell’ottica di un investimento della durata di 15 anni, ha caratteristiche di stabilità maggiori di quelle dell’olio.
|
|
|

|
|
|